Continuous improvement follows one basic philosophy.
No improvement is made without knowing how the current system operates.
Reliability Baselining

MEASURE WITH QUANTITATIVE EXERCISES
Hard work is dedicated to improve maintenance and reliability world-wide. Many react to urgencies based on what some think are problems, but struggle to provide actual change.
Baselining provides clear answers to elusive questions
-
What is the maintenance productivity today?
-
Where are the constraints in the maintenance process?
-
How effective is the planning & scheduling effort?
-
What is the cost of our un-optimized PM's?
-
What is the average cycle time for each step of the workflow?
-
What percent of reactive maintenance was preventable?
-
What is the difference between PM compliance & PM effectiveness?
-
How effective are your predictive maintenance efforts?
-
What true downtime and OEE opportunities exist?
-
What is the value of 1% of improvement?
What about proven tools that can validate the current state of your program?
What if we measure change, turning theoretical savings into hard data?
What if we brought awareness to challenge what is consider "normal"?
SEAM Group’s toolkit of baselining activities can be deployed independently in PM Optimization, Workflow Optimization (planning & scheduling), PdM Programs, TPM, OEE Optimization & Cultural Readiness.
-
Master Planning and Strategic Design Workshop
-
Maintenance Productivity Case Studies
-
Workflow & Reliability Simulation
-
PM Optimization Model Study
-
PdM Program Design & Deployment
-
Planner & Supervisor Utilization Studies
-
Reactive Maintenance Prevention Analysis
-
Mobile OEE Data Validation Studies
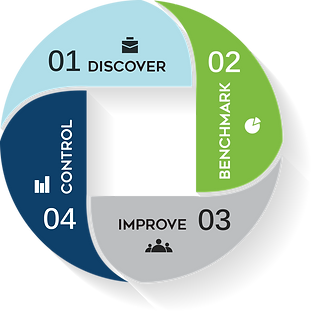
Baselining activities are found in Step 2
of our continuous improvement process.
Contact Us for
Maintenance & Reliability
Baselining!
RELATED LINKS
Workflow Optimization
Craft productivity is the fuel for your entire maintenance & reliability program and it is where value can be achieved. Our Workflow Optimization encompasses a total value-stream approach, addressing losses found in each stage of workflow.
PM Optimization
PM Optimization removes waste and ensures all PM tasks add value and addresses known failure modes. Our comprehensive approach to PM Optimization expands beyond task optimization to encompass a program focused on overall system change.
TPM Operator Care
Our consulting professionals can help you with your organization's cultural transformation toward total equipment management where everyone in the organization shares accountability for reliability.