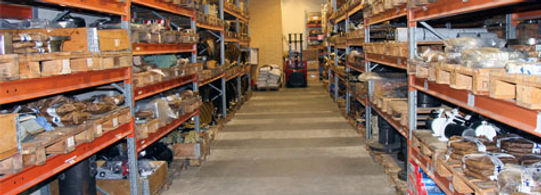
Whether you are working on projects to prevent what could happen or need answers to what actually happened, our reliability process addresses the problem from all angles.

Specialty Services
Reliability – Specialty Services
SEAM Group uses a total approach towards advanced reliability including proven tools and training that brings a new solution to an old problem. The services below can be deployed individually or as part of an overall reliability improvement initiative. Click the links below to learn more.
Root Cause Failure Analysis (RCFA)
Failure Modes & Effects Analysis (FMEA)
MRO Inventory Management
Reliability Centered Maintenance (RCM)
Return on Investment (ROI) Tool
Equipment Criticality Assessment Tool
Maintenance e-Learning
Work Management Simulation℠
Talk to a reliability expert today.
Root Cause Failure Analysis (RCFA)
Root Cause Failure Analysis (RCFA) is a structured process that uncovers the physical, human, and latent causes of any undesirable event. The service determines why the failure occurred and how future failures can be eliminated or prevented. Predictive Service designs and implements a continuous RCFA process to address “bad actors”. Appropriate triggers will be set to initiate future RCFA events based upon tracking failure data from work history or PdM results.
Benefits:
-
Reduced maintenance costs
-
Improved equipment reliability & availability
-
Eliminates recurring problems
-
Sets continuous improvement triggers to identify assets needing RCFA
-
Reduces unplanned failures from occurring
Failure Modes & Effects Analysis (FMEA)
Many maintenance organization’s strategies consist of “fix it after it breaks” (reactive) or “fix it before it breaks” (preventative). However, progressive organization desires a strategy of “don’t fix it, eliminate the failures”.
A Failure Mode and Effects Analysis (FMEA) provides the insight to possible issues that affect the reliability of these important asset. FMEA is a structured risk-based methodology for determining critical equipment functions, functional failures, assessment to causes of failures and their effects. The purpose is to understand the failure modes and their effects in order to design a mitigation strategy to redesign, reengineer or completely eliminate the failure mode. If elimination of the failure mode is not possible or practical, then addressing the failure with another appropriate action is detailed.
Benefits:
-
Complete understanding of the issues from potential failures of critical assets
-
Improved maintenance approach for your most important equipment
-
Understanding the Mean Time between Failure (MTBF) and corresponding maintenance needs
-
Improved reliability and availability of your key assets
-
Reduced maintenance costs
MRO Inventory Management
Effective inventory management is about knowing what is on hand; where it is used, how often is it used and the lead time to acquire. Inventory management is the process of efficiently overseeing the flow of parts in and out of inventory. The process involves controlling the levels to prevent the inventory from becoming too high, or dwindling to levels that could put maintenance and operation in jeopardy. Inventory management seeks to control the costs associated with the inventory, from the total value of the parts, the cost of individual parts and the burden to the organization generated by the cumulative value of the inventory.
Whether you are looking to decrease the total cost of inventory, reduce the dependency on OEM parts or develop a site, regional or corporate parts management strategy, Predictive Service expertise can help put a strategy in place to control costs while ensuring part our available when needed.
Benefits:
-
Identify critical spares
-
Set proper min/max levels and reorder points
-
Analyzed usage patterns for quality control
-
Evaluate vendor partnering and regional strategies
-
Reduce the cost of premium OEM parts
Reliability Centered Maintenance (RCM)
Our RCM process follows the following seven questions:
-
What is the item supposed to do and its associated performance standards?
-
In what ways can it fail to provide the required functions?
-
What are the events that cause each failure?
-
What happens when each failure occurs?
-
In what way does each failure matter?
-
What systematic task can be performed proactively to prevent, or to diminish to a satisfactory degree, the consequences of the failure?
-
What must be done if a suitable preventive task cannot be found?
Benefits:
-
Increase in maintenance cost effectiveness
-
Improved machine uptime
-
Improved understanding of risk your organization is managing
Return on Investment (ROI) Tool
When developing or enhancing an improvement strategy for maintenance and reliability, one key factor always emerges, the need for creating a business case or cost justification. Many times, we can estimate the savings or project the costs, but rarely both. Without both, a true return cannot be calculated, resulting in a less than desirable business case.
The Predictive Service ROI tool guides you through a process of collecting the necessary data from your existing systems to calculate a true return on investment. The tool allows for site specific variables so the resulting numbers are meaningful to your exact situation. The tool helps create “what if” scenarios to ensure all of the stakeholders are comfortable with the effects of implementation cost versus project returns.
The tool provides the quantitative portion of a maintenance initiative and helps in determining the priorities among the key elements in establishing an improvement program, including:
• PM Optimization
• Predictive Maintenance
• Inventory Management
• Work Management
Benefits:
-
Projects implementation costs and benefit over a five year period
-
Establishes and managing key performance indicators
-
Provides a cash-flow analysis summary and individualize for each initiative
-
Identifies the resources required to establish and maintain each initiative
-
Based on real or estimated site specific data to make results more meaningful
Equipment Criticality Assessment Tool
Determining equipment criticality is the first step in most maintenance and reliability improvement initiatives. For many years, maintenance has been applied across all assets with little to no consideration for its importance to the facility’s operation. An informal decision was made to prioritize work based on the assets importance but rarely was criticality applied to the overall maintenance strategy. An equipment criticality assessment by itself is meaningless unless it is integrated into the overall maintenance and reliability strategy. The goal is to focus the majority of your maintenance and reliability investment on critical assets, and adjust it down for those assets deemed less important.
Predictive Service’s Equipment Criticality Assessment tool aids in both a ranked scoring of each asset, and based on those results, tools for planning a reliability deployment.
Benefits:
-
Determine which equipment is most important to the overall success of the facility
-
Establish each assets appropriate maintenance attention and cost
-
Understand where maintenance and reliability issues exist
-
Identify candidates for PdM applications and build a program scope
-
Identify candidate for reliability improvements techniques
e-Learning Continuous Education for Maintenance Skills
e-Learning is an affordable training solution focused on continuous education in support of process improvements delivered through a Predictive Service consulting engagement. e-Learning is a series of training modules available for PM and Workflow Optimization.
Predictive Service offers unlimited access to training solutions for company-wide team development. Consistently train your team to become subject matter experts, able to affect real and permanent change in your organization. LEARN MORE
Work Management Simulation℠
WMS is an innovative, interactive means to transfer the concepts of effective maintenance work management and identify inefficiencies in your work process. The maintenance training simulation addresses unclear job scope, absence of documentation, poorly managed spare parts system, every job being equal in priority and little maintenance job history. As each round unfolds, changes are made to improve the way we manage maintenance work. LEARN MORE
Reliability Baselining
Compare the current state of your maintenance program and processes to available benchmarks and best practices. Predictive Service’s Baselining quantifies and validates performance gaps so improvement initiatives can be scoped and a business case developed.
Reliability Snapshot
Looking to improve your reliability strategy and tired of “fighting fires?” With Predictive Service’s Reliability Snapshot, you gain access to our unique, blended approach to evaluation that assesses your areas of strength and opportunities for improvement.
OEE Optimization
Poor Overall Equipment Effectiveness Optimization (OEE) can have a profound negative impact on your entire operation. OEE Optimization uses a blended approach of constraint management coupled with LEAN principles.